Publicado: August 2nd 2016
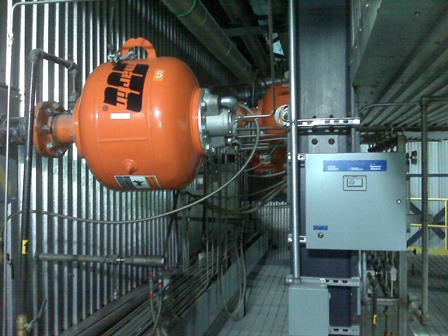
An innovative Minnesota energy company has eliminated labor-intensive air lancing to clean biomass ash from boiler walls by installing a series of high-powered air cannons to dislodge accumulations and restore process flow. The air cannon network at Koda Energy (Shakopee, MN) helps the facility avoid the daily shutdowns and maintenance hours that manual cleaning required, allowing the facility to run at its rated capacity. Programmed to fire in a prescribed pattern, the system from Martin Engineering is fully automated, but can be fired manually if build-up becomes evident through the view ports.
“Efficient material flow is a critical element of biomass-fired boilers, and accumulation or blockages can take a big bite out of a plant’s efficiency,” explained Martin Engineering Service Technician James Millis. “Ash build-up on furnace walls and tubes can choke the process, degrading equipment performance and introducing the potential for safety risks during cleanout.”
Koda’s combined heat and power (CHP) plant burns approximately 500 tons of biomass fuel each day to generate a capacity of 24 MW per hour. A partnership between Rahr Malting Company (RMC) and the Shakopee Mdewakanton Sioux Community (SMSC), the plant is ideally located next to the malting facility, where a consistent supply of biomass fuel is readily available.
The generating plant uses 100 percent biomass fuel in a McBurney high pressure biomass boiler with an output of 220,000 pounds of steam per hour. The electricity generated via turbine serves Koda Energy as well as the adjacent Rahr Malting plant.
Approximately half of the power generated is sold to Xcel Energy, while waste heat from the boiler is recycled back to Rahr, replacing the natural gas previously used in the malting process.
When maintenance crews noticed significant build-up early in the plant’s operational life, they first addressed the issue using a special fuel additive that was purported to reduce furnace fouling, but the results were disappointing. “We found the additive approach to be expensive and largely ineffective,” said Koda’s Chief Engineer and VP of Operations Stacy Cook.
Instead, the company turned to manual cleanout techniques using an air lance. The method was more successful at removing the ash, but it required a daily work stoppage to complete the time-consuming process. “Daily air lancing did remove the build-up, and helped us maintain full output, but we couldn’t reach all areas within the boiler,” Cook continued.
“It also affected our production schedule and posed a potential safety risk for plant personnel,” he said. “To make matters worse, we were facing the possibility of a monthly shutdown to thoroughly clean out the boiler.”
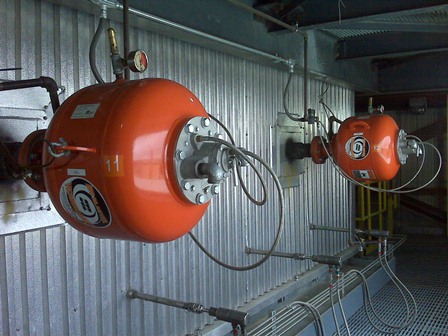
An Air-Powered Solution
During a visit from Martin Engineering to explore the use of air cannons in another part of the process, Cook reviewed the fouling problem and asked whether the technology might be useful for preventing ash build-up on the boiler walls and tubes. “We decided to try the air cannons first for cleaning those areas that were inaccessible with a hand lance,” Cook explained. “Our thought was that it would be a good way to gauge how effective they might be for this application.”
The initial installation showed promise as a way to eliminate the hand lancing, and together with Martin Engineering technicians, Koda developed a plan to expand the air cannon system. Over the course of three planned maintenance outages, Martin Engineering crews installed a total of 12 Martin® Hurricane Supreme Air Cannons.
Introduced by Martin Engineering in 1974, air cannon technology has since developed a proven track record around the world for relieving bottlenecks caused by material buildup in high-capacity storage and process vessels.
The Hurricane Supreme Air Cannon is a positive-acting, internal valve design from Martin Engineering, developed specifically to deliver maximum force output from a very direct air path, requiring minimal air consumption and a small footprint. By producing more power from less air, it uses a smaller reservoir, which in turn allows the Hurricane to fit into smaller spaces.
By activating the solenoid valve, a positive pressure signal is sent to the Hurricane’s exhaust valve, causing it to actuate and release the pressure holding the piston. The piston is instantly forced back by the air pressure stored in the tank, and the blast of air is then directed through the nozzle and into the boiler.
Because it fires only in response to a positive surge of air sent by a solenoid, the Hurricane valve will not discharge accidentally in response to a drop in pressure, such as might occur from an air supply failure or broken line. The specially-designed valve allows the control solenoid to be positioned as far as 200 feet (60 meters) from the tank, helping to keep solenoids away from harsh environments and difficult service conditions.

“Before we installed the air cannon system, we had to manually air lance the boiler every day to maintain adequate heat transfer in the wall tubes,” Cook continued. “Since the installation was completed, we’ve been able to maintain full boiler output without any hand lancing,” he said. “That has allowed us to keep the boiler wall surfaces clean, while avoiding the manpower requirements and potential hazards associated with hand lancing. We can now run the system at its rated capacity, without the negative effects previously posed by boiler fouling.”
The operation has been so successful that the Minnesota High Tech Association (MHTA) named General Mills and Koda Energy as finalists in the Innovation Collaboration of the Year category for the 2010 Tekne Awards. The Tekne Awards recognize Minnesota companies and individuals who have shown superior technology innovation and leadership.
“If they become severe enough, flow problems can bring operations to a complete stop until the problem is corrected,” Millis added. “Although many facilities still use manual techniques to remove boiler build-up, the costs of labor and production shutdowns have prompted some plants to investigate more effective methods for dealing with this type of flow issue.”