Publicado: August 2nd 2016
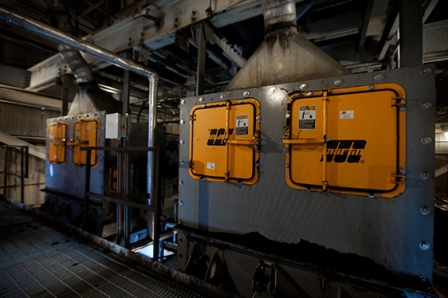
Westar Energy is the largest electric utility in Kansas, with 19 energy centers providing 7,100 MW of generating capacity to serve more than 689,000 customers. The firm employs about 2,400 people and operates approximately 35,000 miles of transmission and distribution lines. Westar maintains four coal-fired facilities, the largest of which is the Jeffrey Energy Center (JEC) near St. Marys.
Situated on 10,500 acres of land, JEC is the largest coal-fired power plant in the state, with three generating units producing 1,857 MW, ranking it the 19th largest in the nation. The first unit came online in 1978, and the newest in 1983. All three burn low-sulfur coal (as much as 33,000 tons per day between them) and take advantage of some of the most advanced emission control technologies available.
JEC was named the Powder River Basin Coal Users Group Plant of the Year in 2003, and was the first facility in the four-state region to receive the OSHA VPP Star designation in 2007. The site includes three wildlife management areas and 7,700 acres that are leased to local farmers.
Material Handling Challenge
Over time, operators at JEC began to notice increased dust and spillage around four transfer points on four of its 42-inch conveyors. The problem was traced to worn chutes and skirtboard liners, which no longer contained the coal fines as they did when new. A worn-out skirtboard liner plate was found to be exacerbating the problem.
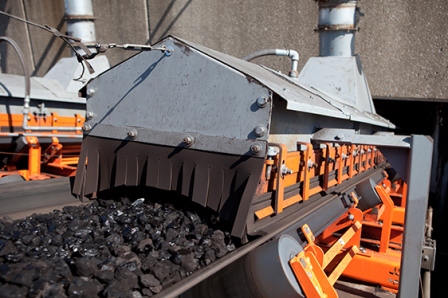
“We have two transfer buildings where the yard feeders deliver incoming material to supply the boilers,” explained Coal Handling Engineer Josh Olson. “They were wearing out, and we knew we needed to take action. But rather than patching the existing chutes and liners, we wanted to see if we could find a better design solution.”
The ½-inch thick belts on conveyors 101A, 101B, 301A and 310B travel 550 FPM and have a capacity of approximately 1,000 tons per hour. The load is 4" minus PRB coal, with a moisture content around 28-30% and bulk density of 45-55 pounds per cubic foot.
Westar contacted Martin Engineering to investigate its options, and technicians came out to assess the situation. “Chute design has evolved since this system was first installed,” observed Martin Engineering Territory Manager Jason Illum. “Today’s engineered flow chutes employ special geometries that capture and concentrate the material stream as it travels through the chute.
“Every design is tailored to suit the specific material characteristics and conveyor systems of the individual customer, rather than using stock products and attempting to make them work,” he explained. Transfer Chutes from Martin Engineering provide the dual benefits of minimizing aeration and preventing buildup within the chute, particularly important when dealing with combustible materials.
After reviewing the proposed re-design, Westar engineers visited a nearby facility in which Martin Engineering had installed a similar system. “We were very impressed by what we saw,” Olson continued. “The conveyors delivered excellent belt support, and the material flow was directed to minimize turbulence and maximize dust containment.”
Engineered Flow Transfers
The engineered chutes designed for the Westar facility employ a “chute and spoon” transfer, with the head discharge chute at the top of the system and a spoon receiving chute to place material with minimal impact onto the belt being loaded. Martin Engineering components are custom-designed to suit the characteristics of the conveyed product and the materials used for chute construction.
“The head chute design allowed for external mounting of the head pulley bearings, replacing the old design,” Illum said. “The spoon provides a curved loading chute for a smooth line of descent, consistently feeding the material at a specific speed and direction to minimize impact in the loading zone.”
The goal is to confine the material stream and reduce air entrainment, while directing the moving load onto the receiving belt with minimal impact. Successful designs reduce spillage, belt abrasion, dust and chute wear. This control also helps ensure that material is center-loaded on the belt, avoiding mis-tracking and fugitive material.
To achieve the optimum chute, spoon and settling area, the engineered flow chutes from Martin Engineering were designed using 3-D computer-based flow and modeling to define the geometry. System designers used detailed information about the specific material characteristics and the parameters of the conveyor system itself, including the feed system, belt properties, support structure and transfer distances. By controlling the velocity and force of impact in the load zone to match the belt speed and direction, the engineered systems mitigate material splash, turbulence and dust.
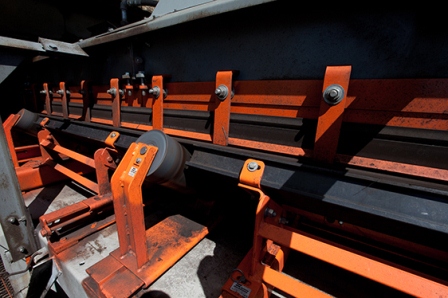
Low-impact loading and controlled airflow can help eliminate the need for baghouse dust collection systems, and the stable material path contributes to improved transfer, while minimizing belt abrasion and spillage. Potential spillage is further contained by eliminating belt sag and providing effective sealing at the belt edge. All four transfer points also received Martin Engineering belt cleaners to minimize carryback.
“One of the features that our operators and mechanics really like is the adjustable skirtboard,” Olson said. “We can get very precise sealing, and the reversible design of the ApronSeal™ gives us double the service life. When one side wears out, we can just flip it over. It may seem like a simple idea, but it shows that Martin is ahead of the curve with its products.”
Martin® ApronSeal™ Skirting was the first dual-sealing system on the market, incorporating a primary seal clamped to the steel skirtboard to keep lumps on the belt and a secondary or “outrigger” strip to capture any fines or dust particles that pass beneath the primary seal. The secondary seal lies gently on the belt and self-adjusts to maintain consistent strip-to-belt pressure, despite high-speed material movement and fluctuations in the belt’s line of travel.
“Another deciding factor for us was the no-excuses guarantee,” Olson added. “We didn’t want to have to spend a lot of time tweaking the system. The Martin Engineering guys are extremely knowledgeable, and they’ve been out several times to make sure everything is running at its optimum level.”
Since the transfer chute overhaul was completed in 2011, results have been excellent. “We don’t take specific measurements or airborne dust readings, but we can definitely tell that the load is centered, spillage is significantly reduced and dust is being contained,” Olson concluded. Quarterly inspections and reports are provided by Martin Engineering for one year at no cost to JEC.