Publicado: August 2nd 2016
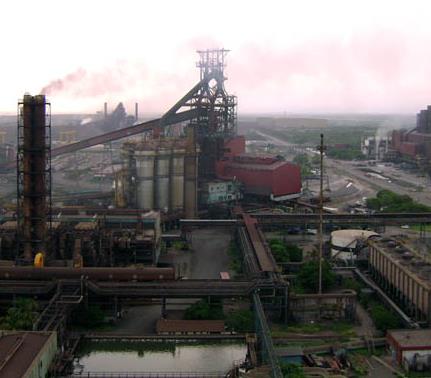
Lázaro Cárdenas is a port city located in the southern part of the Mexican state of Michoacán. The area enjoys a mostly desert climate and receives very little precipitation with the exception of a rainy season beginning in August. Lázaro Cárdenas is also home to a deep-water seaport that handles container, dry bulk and liquid cargo. In addition, the port exports automobiles from various Mexican assembly plants to markets in Southeast Asia and South America. The port handled 1.24 million TEU in 2012 and is expanding to a capacity of 2.2 million TEU annually.
Lázaro Cárdenas is also an important hub of the steel industry in Mexico. Arcelor Mittal Lazaro Cardenas is Mexico’s largest steel producer and slab exporter. The company is the only dedicated slab producer in the world using the DRI-EAF continuous casting method as its primary metallic input for steelmaking. This process results in higher quality slabs with a uniform grain structure and superior finish – thereby offering more benefits to the end user.
During the rainy season, Arcelor Mittal noticed an increased buildup in the bulk material handling processes at the Lazaro Cardenas plant. Accumulation was forming on the walls of the hoppers, causing a continual headache for operating personnel and a consistent bottleneck in the production process. To knock down the buildup, operators resorted to hitting the vessel walls with heavy tools in an effort to dislodge the buildup from outside the vessels. The tactic brought marginal benefit, however, and the frequent production downtime to clean out the blockages was proving to be very costly, causing the plant to incur higher labor expenses, shortened refractory life and reduced process efficiency.
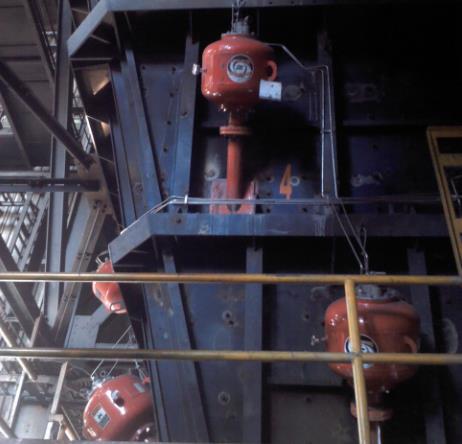
Arcelor Mittal contacted Martin Mexico, a leading bulk materials solutions provider in Latin America. Martin Mexico recommended a series of air cannons for each vessel to help solve the problem. The air cannon (also known as an air blaster) has proven itself over three decades of use, demonstrating its effectiveness as a flow aid device in cement manufacturing, coal handling and other industries. Applications vary widely, from emptying stagnant bulk material storage vessels to purging boiler ash to cleaning high-temperature gas ducts.
The two basic components of an air cannon are a fast-acting, high-flow valve and a pressure vessel (tank). The device performs work when compressed air (or some other inert gas) in the tank is suddenly released by the valve and directed through a nozzle, which is strategically positioned in the tower, duct, cyclone or other location. Often installed in a series and precisely sequenced for maximum effect, the network can be timed to best suit individual process conditions or material characteristics.
In many applications, this engineered firing sequence will relieve the build-up problems. The air blasts help break down material accumulations and clear blocked pathways, allowing solids and/or gases to resume normal flow. In order to customize the air cannon installation to the service environment, specific air blast characteristics can be achieved by manipulating the operating pressure, tank volume, valve design and nozzle shape.
A total of 68 Martin® Air Cannons were installed on a total of 10 hoppers at the Lazaro Cardenas facility. With the powerful discharge from the reservoir of compressed air, the air cannons successfully removed the caked-on material from the hopper walls.
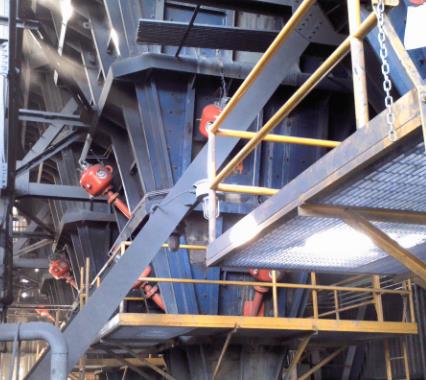
Martin® Hurricane Air Cannons are designed for simple maintenance. The complete valve assembly can be removed in one easy step, working from one side of the tank. It can be replaced within minutes to keep downtime to a minimum, and there is no need to remove the tank from the vessel for service, a significant advantage when they are installed in confined places. The entire air cannon system at Lazaro Cardenas ? including blowpipes, air lines and control systems ? was installed by a MartinPLUS® Service Team.
To maximize their effect, the air cannons were strategically installed in a series and precisely sequenced to dislodge the accumulation and resume normal flow. The network is timed to suit the plant’s specific process conditions and material characteristics. The timed discharge of the air cannons discourages accumulation that impacts process efficiency and raises maintenance expenses, while helping minimize process interruptions and manual labor. Since the installation of the air cannons, the plant has virtually eliminated the need to manually clean the hopper walls. The customer can operate the air cannons from the control room and maintain operational efficiency.